Guide to Calculating Heat Duty in Storage Tanks
Ing. José Félix Acevedo B.
5/7/20253 min read
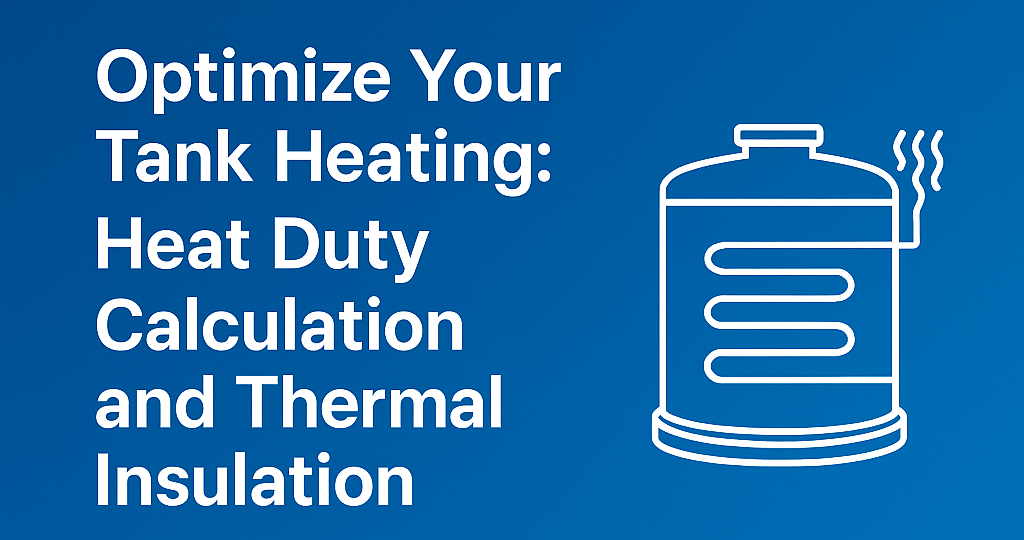
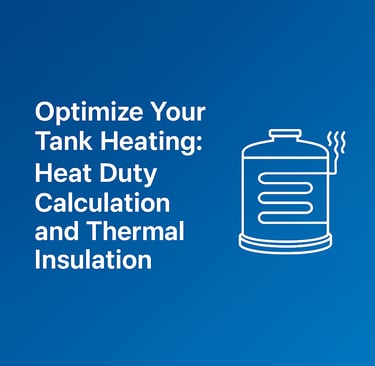
1. Introduction
Heat duty is a critical parameter in the thermal design of storage tanks, especially for viscous fluids such as asphalt, heavy fuel oils, greases, or resins. Accurate thermal calculations ensure product operability, optimize energy consumption, and improve overall system efficiency.
2. What is Heat Duty?
Heat duty refers to the amount of heat that must be transferred to the tank contents in order to:
Maintain a constant temperature
Raise the product temperature from its initial to the desired value
Compensate for heat losses to the environment
This value, typically expressed in kilowatts (kW), forms the foundation of any thermal system design.
3. Key Parameters for Calculation
3.1 Fluid properties:
Stored volume (m³)
Density (kg/m³)
Specific heat capacity (kJ/kg·°C)
Initial and target temperature (°C)
3.2 Environmental conditions:
Ambient temperature
Heat losses through convection and radiation
3.3 Tank configuration:
Exposed surfaces (bottom, walls, roof)
Presence and type of thermal insulation
3.4 Heating time available:
Based on operational or design conditions
4. Required Heat Calculation
To raise the temperature of the product, the following equation applies:
Q = m × Cp × ΔT
Where:
Q = total heat required [kJ]
m = product mass (volume × density) [kg]
Cp = specific heat capacity [kJ/kg·°C]
ΔT = temperature difference (°C)
5. Conversion to Thermal Power (Heat Duty)
To express heat duty as power:
q = Q / t
Where:
q = required heat duty [kW]
Q = total heat required [kJ]
t = available heating time [s]
6. Importance of Thermal Insulation
Tank insulation is key to reducing the heat duty required. An uninsulated tank has high thermal losses, which means higher energy consumption.
Without proper insulation:
Heat losses are high
More energy is needed to maintain the target temperature
Operating costs increase
With good insulation:
The overall heat transfer coefficient (U) is reduced
The required energy input decreases
Energy efficiency and temperature stability improve
Heat losses can be estimated with:
Q_pérdidas = U × A × (T_producto − T_ambiente)
Where:
Q_losses: heat loss to the environment (W)
U: overall heat transfer coefficient (W/m²·K)
A: exposed tank surface area (m²)
T_product: stored fluid temperature (°C)
T_ambient: outside ambient temperature (°C)
Lowering U through effective insulation directly reduces heat duty.
7. What Happens When Insulation Thickness Increases?
The global U-value decreases:
A thicker insulation layer increases thermal resistance and reduces heat transfer to the environment.
Thermal losses decrease:
Less energy is needed to maintain the product temperature.
Energy efficiency improves:
Lower steam or thermal oil consumption results in long-term savings.
Thermal stability increases:
The fluid retains its temperature longer during system shutdowns or maintenance.
However:
o Insulation costs and volume increase
o Marginal gains decrease as thickness increases
o A technical-economic balance must be found
8. Thermal Insulation: Conductivity, Thickness, and Efficiency
Heat transfer through insulation is described by:
Q = k × A × ΔT / e
Where:
k = thermal conductivity [W/m·K]
A = exposed surface area [m²]
ΔT = temperature difference between fluid and environment
e = insulation thickness [m]
👉 The lower the conductivity and the greater the thickness, the lower the heat loss. However, beyond a certain point, increasing thickness further is not cost-effective.
9. Common Insulation Materials for Storage Tanks
Mineral wool:
Thermal conductivity: 0.035–0.045 W/m·K. Max. temp.: ~600 °C. Cost-effective, fire-resistant, durable.
Polyurethane foam (PUR):
Thermal conductivity: 0.022–0.030 W/m·K. Max. temp.: ~120 °C. Excellent insulator, hydrophobic, lightweight.
Polyisocyanurate (PIR):
Thermal conductivity: 0.020–0.025 W/m·K. Max. temp.: ~150 °C. Higher thermal stability than PUR.
Foamglas® (cellular glass):
Thermal conductivity: 0.038–0.055 W/m·K. Max. temp.: ~430 °C. Non-combustible, impermeable, and chemically resistant.
10. Common Industrial Insulation Systems
External insulation:
Applied directly over the tank surface. Typically consists of insulation material, a vapor barrier, and metal cladding (aluminum or stainless steel).
Sprayed or injected foam:
PUR applied directly to the tank’s external surface. Ideal for compact systems or irregular geometries.
11. Conclusión
Accurately calculating the heat duty, along with selecting a suitable insulation strategy, allows you to define energy requirements clearly, design an efficient thermal system, and reduce operational costs.
Details
engineering
info@aceinteca.com
© 2024. All rights reserved.
Technical Information for Tank Equipment Courtesy of World Bridge Industrial Co. Ltd.
Technical Information for Tanks Protection Devices Courtesy of Korea Steel Power Corp.
Technical Information for Bolted Tanks Courtesy of Center Enamel.
Glass Fused Steel Bolted Tanks
Stainless Steel Bolted Bolted Tanks
Aluminum Suspended Deck for Cryogenic Tanks.
Aluminum Rolling Ladder for External Floating Roofs
WhatsApp +58 416 6289796